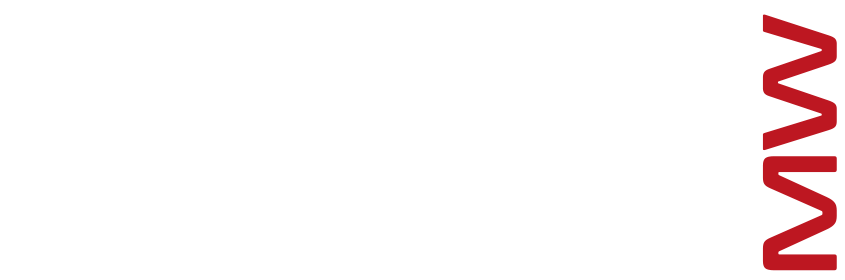
719MW DRIVER – Q&A WITH TOM WISHON
Is the 719MW the first adjustable weight driver Wishon Golf has designed?
No, while my status as a senior citizen is making it difficult to remember every model I have designed in my career, I do remember that the 739CCG in 2012 and the 939AHT in 2015 both were designed with a single weight port in the rear center back of the heads that accepted different screw in weights. However, the heaviest weight was 16g and being only in the rear center back, it could only have a small effect on increasing launch angle, and only for players with a later to very late release.
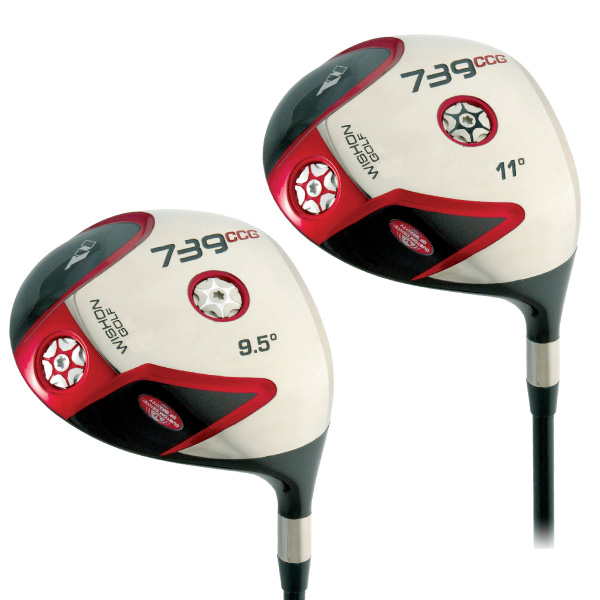
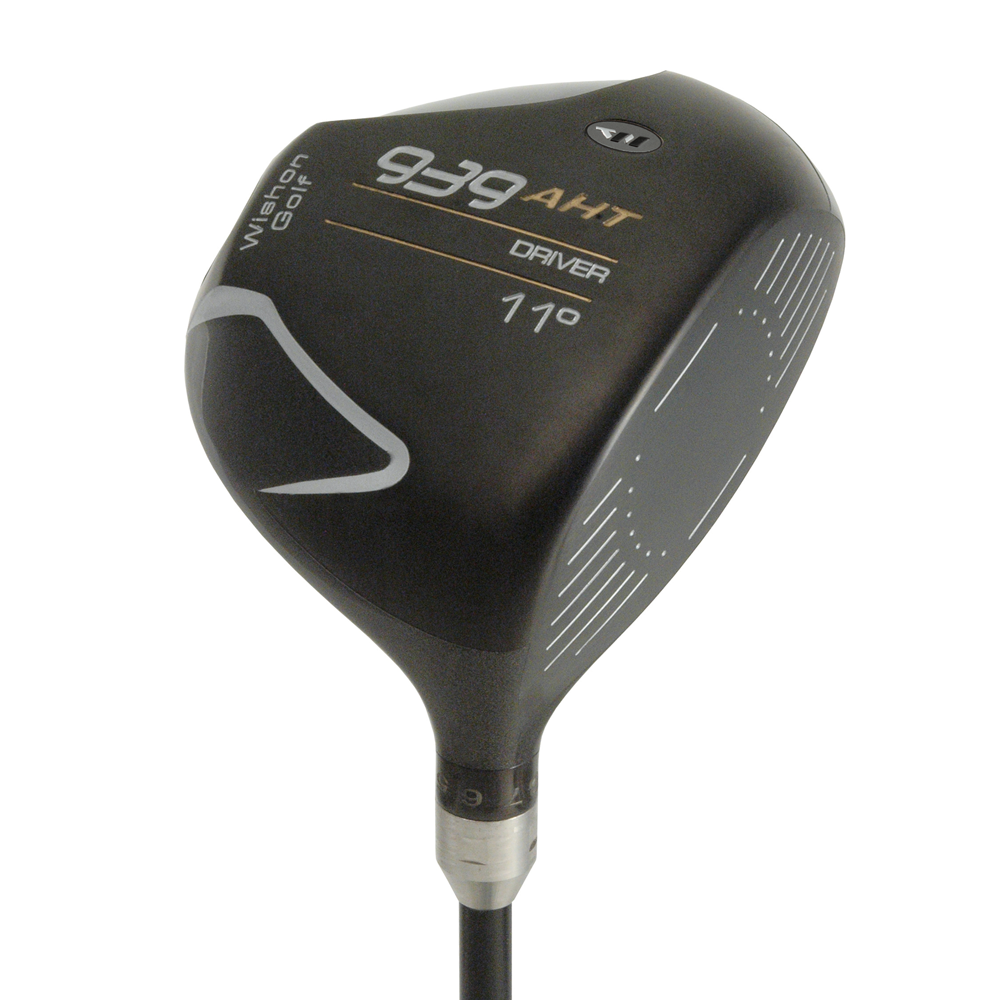
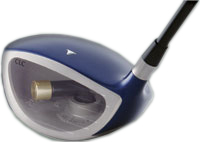
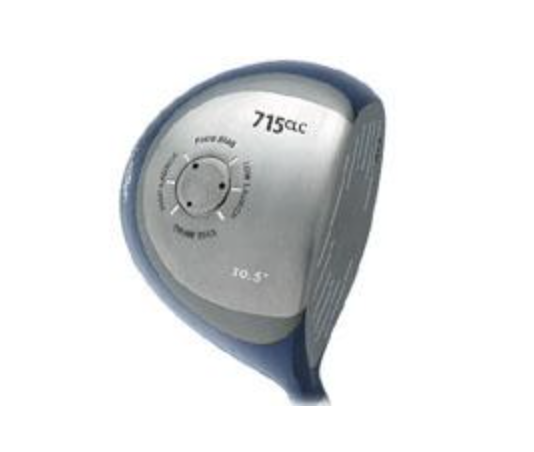
Can you explain a bit about the lengthy design process for this model and the obstacles that came alongside it?
My normal driver head weight has been 202g for a long time. Other companies choose lighter driver head weights than that because they want the drivers to be built to 45 to 46″ lengths. If you have followed any of my work over the years, you would know that I believe that the biggest reason 95% of all golfers have a big problem with driver shot consistency is because all these companies make their drivers too long. WAY too long. I chose a 202g head weight for my drivers because that in essence “forces” (maybe the better word is “encourages”!) clubmakers to build my drivers shorter than 45-46″, which absolutely makes a huge difference for improving driver performance for so many golfers.
So the challenge in going to work on a new movable weight driver head that could allow the movement of at least 30g of weight around the head to change shot shape was quite simply, to make a 450-460cc size driver head body that would weigh no more than 170-172g, and most importantly, which would be completely durable. The only way that could be done was to find a factory that could consistently form a titanium driver body with VERY thin walls to keep the weight down, but at the same time, to be extremely tight for achieving the necessary strength and toughness.
The other challenge in this was to design the head in a way to use less titanium to create a functional and cosmetically appealing shape. Let me elaborate to explain this: out in the industry you have seen many drivers with elaborate channels in which a weight can be made to slide from one side of the head to the other. Such a channel shape requires a lot of surface area of titanium, which uses up more weight. We only had a maximum of 172g to play with in making the 450-460cc size of the 719MW driver body. This is why we ended up creating four, compact size recessed cavities in the toe, heel, front and back areas of the 719MW sole, instead of weight sliding channels.
And finally, I chose to make the driver by investment casting, not the usual 4-piece construction that I have used in every previous WIshon driver – well, except the 715CLC, which was investment cast in our attempt 16 years ago to make the largest head body size that could accept up to a 40g weight arm. With investment casting, it is possible to vary the wall thickness of the body to be as judicious as possible with the weight of the titanium. But casting titanium with precision is VERY difficult, chiefly because, a) titanium’s extreme reactivity with oxygen requires it to be cast in a vacuum, and b) molten titanium has the viscosity of molasses and is very difficult to force into very thin wall sections in a casting shell. In short, I needed the very best titanium casting factory in the world to do this project for me. And the problem with that was that all of the titanium casting factories that I was aware of that were accomplished enough to attempt this project were companies that only do work for golf companies that place orders in quantities of hundreds of thousands to millions of heads per year.
And then came an absolute stroke of serendipity. One day when I was obsessing about how was I going to get a 450-460cc size head body made to a weight no more than 172g, an email popped into my inbox from a man who identified himself as the owner of an investment casting factory owner I had not previously heard of. Long story short, this man contacted me to say he wanted to do a design project with me because back in the 80s when he was a supervisor for a large clubhead production factory, I had been his teacher.
From 1986 to 1993 I served as president of Dynacraft Golf Products, which during this time we grew into being the second largest component clubmaking supply company in the US, behind Golfsmith International. Dynacraft was 50% owned by Dynamic Precision Casting Corp., which was then and is still today one of the largest clubhead production factories in the world. Starting in 1986 when I went to work for Dynacraft, the owner of Dynamic Precision would have me come over to his factory many weeks each year to not only work on the head design projects for Dynacraft, but to teach his technical staff anything and everything I knew about golf clubs.
The man I found in my inbox that day was one of my former “students” who went on to build his own clubhead production factory. Over the years his factory had quietly become a major supplier for several of the large OEM companies, specializing in precision investment casting of titanium alloys. As a “thank you” of sorts for the help I had given to him through my weeks of teaching in the late 80s to early 90s, he wanted to open the doors of his factory to help me with any design project I might have.
Thus by fortune, the door was opened to be able to create the 719MW driver head.
The total adjustable weight being 30g – this is more than most OEM adjustable weight drivers. Can you elaborate on the decision behind this?
I have a lot of history well before starting the Wishon Golf brand with designing heads with weight positioned around the head in an effort to elicit a change in shot shape. If you are interested in the history of golf club technology, a must read is the original 1968 book, The Search for the Perfect Swing, by Alastair Cochran and John Stobbs. Cochran and Stobbs’ book stands as the original milestone in uncovering the beginning of understanding the science of golf club performance.
I still have my original copy that I bought in 1969 when I was a fledgling club repairman, working as a PGA assistant pro at the Mill Valley GC in the San Francisco Bay area. On page 209 of that book is an illustration of a driver head with the authors’ supposition that a movement of weight to the heel side of the head would move the center of gravity toward the heel enough that a shot hit on center would activate the “gear effect” to induce more of a hook, or reduction in a fade.
Fast forward to when I was running Dynacraft and doing all their clubhead designs. In 1988 when I was scanning through my copy of The Search for the Perfect Swing and came across that same heel weighting illustration, I decided I wanted to make such a head to test the theory. To my knowledge no companies had ever created or sold such a head. In 1988 investment cast driver heads were still in their infancy, only cast from stainless steel, and unable to be made any larger than 150-160cc. in short it would be impossible with then current production technology to make a substantially heel weighted driver.
So I turned to Elmore Just, founder of Louisville Golf Company. I already had a business relationship with Elmore. His company made the persimmon and laminated maple wood heads we sold at Dynacraft. And yes, even though stainless woods debuted in the early 80s, wooden woods still sold through that decade. With Elmore, we made a laminated maple driver with a substantial brass weight in the heel that we eventually called The Cure. That was the head that taught me Cochran and Stobbs idea to create a heel weighted driver head to enhance a draw/reduce a fade, was viable. However, the head also taught me that this only provided a visible shot shape change for players with higher clubhead speeds as well as for players who could consistently achieve impact in the center of the face.
Problem was, when we brought this driver head to market, it was when the market was clamoring for metal woods and wooden drivers were on their deathbed. Fast forward to 1995 when I was VP of Golfsmith International, in charge of all product design and development for the company and its various equipment brands. Titanium drivers were in their infancy with the largest titanium driver head being 230cc in volume! Stainless driver heads were limited by the much higher density of steel over titanium. In short it was still impossible to think about creating a heel weighted driver head from either steel or titanium.
So I turned to high grade aluminum, and in 1995 Golfsmith debuted a cast 7075 aluminum driver called The AccuCore 50 that had a large brass weight embedded in the heel side of the head. As happens in marketing, we fudged the mass of the heel weight! While marketing said it was a 50g brass heel weight, in reality it was 41g! In addition, the position of the weight was not in the extreme heel side of the head so its effect to move the CG was limited. But with this larger mass in a head that was larger due to being made from aluminum, we proved that with enough weight you could alter shot shape for average golfers.
From there came the 715CLC for my company in 2007 which eventually begat the 719MW in 2023.
In other words, sometimes it takes a few years for an idea to evolve to a point that it reaches a pinnacle!!
The 719MW also features a custom adjustable hosel sleeve, which is a first for Wishon. What was the thinking behind this?
When the modern adjustable hosel sleeves came out and only professed to change loft, I was completely against this use of a change in the angle of the shaft into the head. Yes a change like that in an iron, done by bending the hosel, is acceptable to change loft because golfers are always, always trained to address the ball with the iron head positioned square to the ball/target. But with woods, the vast majority of golfers make it a habit to rest the driver/woods on their sole before hitting the shot.
Because drivers/woods have a far wider sole than an iron, this is why when a golfer soles the driver/woods, a change of the angle of the shaft into the head as done by the rotation of an adjustable hosel sleeve will only change lie or face angle and not loft. To get the loft change from a modern sleeve requires the golfer to hold the club with the face square and to never let the sole rest on the ground.
Doing that completely eliminates the face angle from being a custom fitting specification for golfers. And since I see face angle as such an important fitting specification for so many golfers, this is why I have never been in favor of an adjustable hosel sleeve for changing loft.
In 2015 I designed the 939AHT driver with an adjustable hosel sleeve, but the sleeve was designed to offer a change in lie or face angle. Not loft. For loft changes we tooled and manufactured different loft models in the 919AHT.
As I went into the design of the 719MW, I realized that my “battle” to eschew adjustable hosel sleeves for loft change was like beating my head against a brick wall. EVERY adjustable hosel sleeve in the industry purports to change loft. Golfers are used to that now. But I still designed the 719MW hosel sleeve to chiefly be a means to customize lie and or face angle. However, as my “form of surrender” I decided to create two charts in the 719MW instruction sheet – one chart tells what sleeve position will result in what lie or face angle change to the head. The other chart tells what loft change you get from each sleeve position with the proviso clearly stated that if you choose to use the sleeve for loft change, you have to hover the club off the ground while being held in a square face position behind the ball. And I clearly state that such use is only for players who have no need whatsoever for a custom face angle other than 0* square.
What are the main differences between the 719MW and other modern adjustable weight drivers?
The 719MW also allows the movement of MORE weight than any other driver on the market. A 30g weight is available for use with the 719MW. To our knowledge no other driver allows that high of a weight mass to be moved around the head to elicit a change in shot shape. And the reason that is important is because for the vast number of average golfers with a driver clubhead speed under 90-95mph, visible shot shape changes cannot happen with a weight movement of less than 25 grams. Few if any of the other movable weight driver heads offer a weight movement of more than 15-20g, if that much.
The 719MW driver is the only driver capable of using multiple weights to markedly increase the Moment of Inertia of the head. By using three 10g weights positioned in the toe, rear and heel sides of the head, it is possible to increase the MOI of the 719MW by over 400 g-cm2. Meaning the 719MW’s MOI can be increased by as much as 7-8%. Even more of an MOI increase is capable if the driver is made to a shorter length such as 43-43.5″ with a very light shaft (45-55g) so that 15g weights can be used in the toe, rear and heel to push the MOI up by 12-15%.
The 719MW driver is the only driver capable of being built to normal ranges of swingweight at lengths that can vary from 39″ to 49″. Starting with a head body weight of 172g and with 4 weight cavities that can accept weights up to as much as 30g, it is possible to make the 719MW head weight anything from 172g up to as much as 292g! Every other driver ever made cannot allow as much of a weight range as does the 719, not even close. Of course, few if any would want a driver with that high of a head weight, but the 719’s custom length capability is completely unsurpassed.
Another unique ability of the 719MW is that it is possible to build drivers to very light swingweight or very heavy swingweight or very heavy swingweight for very weak or very strong players. Recent research we are doing is showing that the old standard C7 swingweight for women or seniors is too head heavy for a lot of these people who are lower in strength or higher in age. Many custom clubmakers have been experimenting with good success with B8 to C4 swingweights for their seniors or women players. No other driver can allow that.
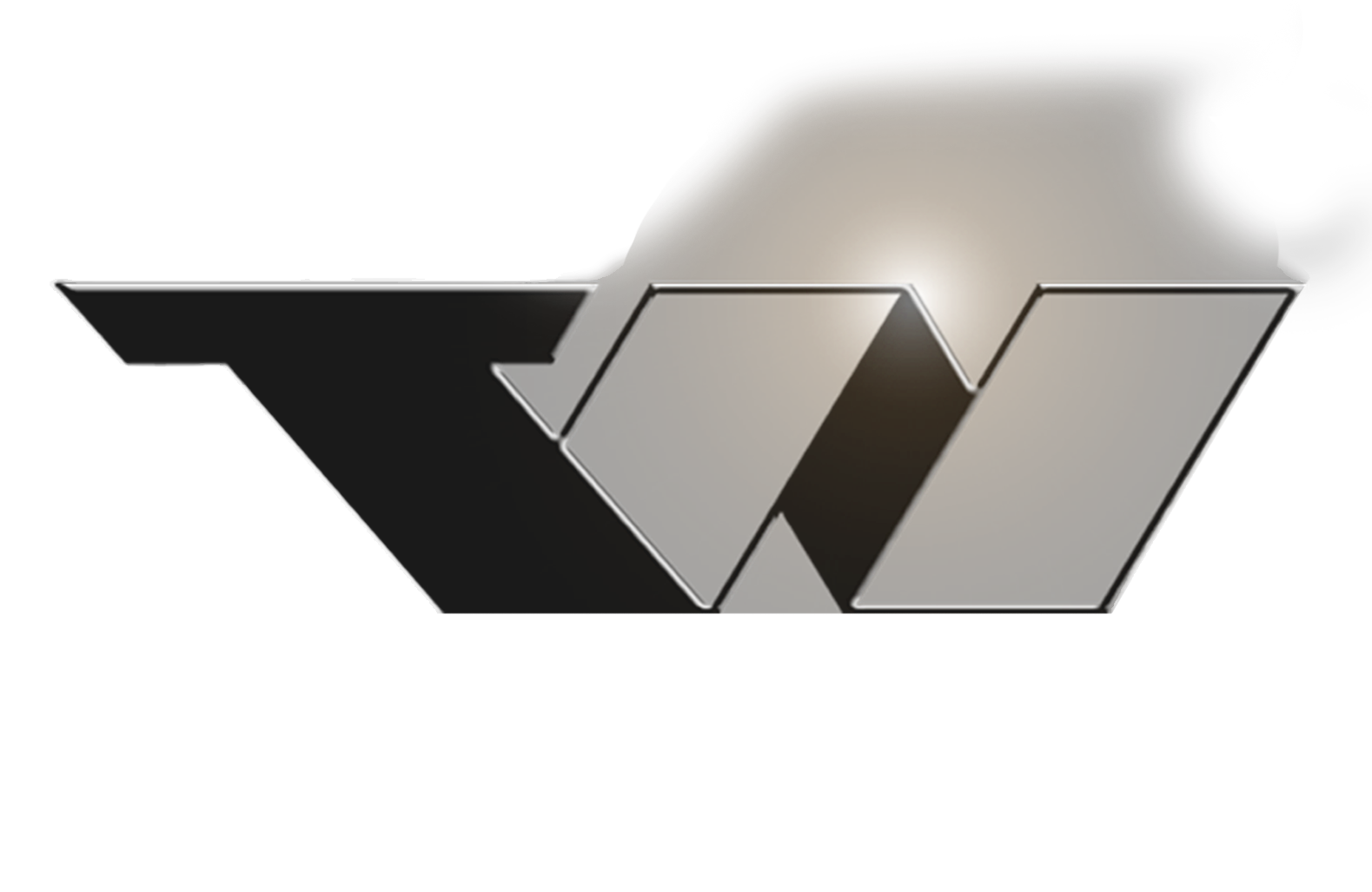
© COPYRIGHT 2024 WISHON GOLF