DESIGN FIRSTS
IRONS
First Injection Molded Polymer Body and Metal Ironhead
1989 – Dynacraft IMI-703 (prototype model only)
Described in US patent #5,333,871, this was the golf industry’s first ironhead produced by injection molding a light and strong polycarbonate material over a heavy steel sole and inner core piece. The intent was to create an ironhead with a very low center of gravity with weight distribution that could be varied much more significantly than in any homogenous metal or multi-metal construction. The model remained an innovative prototype only when the company for which Wishon designed at the time decided not to incur the high cost of injection mold tooling dies to manufacture the full set.
First Vertical Flow Weighted Iron Set
1989 – Dynacraft Genesis Irons
Numerous sets of irons from the mid-1990s to present times which have been created by several of the largest golf companies borrowed the weighting concept of vertically progressing the placement of rear weight from low on the long irons to higher on the short irons from Wishon’s 1990 Genesis iron design. This progressive weighting concept was called Vertical Flow Weighting.
The Genesis irons was the first iron design in the golf industry to introduce vertical flow weighting to keep the center of gravity (CG) low on the low lofted heads to help increase launch angle, and then gradually moving the mass higher in the back cavity through the middle and short irons to prevent hitting the ball too high with the high lofted irons in the set.
First Set of Irons to use Different Steel Alloys for Different Heads within the Same Set
1991 – Dynacraft Vari-Steel Irons
The Vari-Steel, short for variable steel alloys, was designed using 17-4 stainless steel for the body material of the long irons, 431 stainless for the middle irons and 1030 carbon steel for the short irons in the matched set. While most certainly a ‘pain’ for the foundry to manufacture because of the requirement to change steel alloys in the investment casting process and monitor different heat treatment procedures for each segment of the set, the Vari-Steel irons employed the use of three different steel alloys in the same set to offer golfers a difference in ‘feel’ and material hardness through the set.
The design itself incorporated a vertical flow of the mass on the back of the head to keep more mass low on the long irons, graduating progressively to higher mass on the back of the short irons and wedges.
First Set of Irons to combine hollow and solid body construction within the same set
1991 – Dynacraft Innerdyn Irons
Full sets of two-piece, investment cast hollow body irons brought about greater perimeter weighting and movement of the CG further back from the shaft – both proven game improvement features for middle to higher handicap players. However, moving the CG further back from the shaft is not necessary in the higher loft irons, where the loft is enough to enable all levels of golfers to easily get the ball up.
The Innerdyn irons incorporated a combination of hollow body, rear-CG long irons with one-piece, solid body middle and short irons. The Innerdyn recognized that a low and rear-located CG was worthwhile in the longer, less lofted irons, but such a design feature is wasted on the irons where the normal loft increase and length decrease combine to make the iron easy-to-hit. Thus the game improvement features of the Innerdyn were offered were they were needed, not where they were not, and kept the total price of the set more affordable than all hollow iron set designs.
Notably, the Innerdyn irons stand as the forerunner to sets of irons made with hybrid type irons and conventional type irons in the same matched set which was first introduced in the early 2000s by several of the large golf companies.
The Innerdyn irons were also one of the very first irons to be finished in a black oxide impregnation treatment to make the surface finish of the heads black, a type of finish that became popular in the 2010s.
First One-piece of investment cast ironhead with undercut cavity
1994 – Golfsmith RMC270 Irons
Ironheads with an undercut back cavity became a popular offering of many companies in the late 1990s and early 2000s. The RMC270 was an undercut cavity iron design in which metal was ‘scooped out’ from the lower back cavity area of the iron to position weight both lower and farther behind the face for a slightly higher launch and shot trajectory. This model was designed by Tom approximately 5-6 years before undercut irons became a popular style of design with other companies in the golf equipment industry.
First set of ironheads with all Milled faces
1995 – Golfsmith CNC5000 Irons
In the mid-1990s virtually all ironheads were manufactured by investment casting. While investment casting is a very accurate process for repeating specifications and shapes in volume production, the faces of investment cast irons at this time were never perfectly flat. In addition, in the mid-1990s there was a bit of a dispute in the golf industry over V- or U-shaped scorelines and which was better for generating more backspin. (Even though as Tom and others taught, the scorelines themselves have little to do with spin generation!)
The CMC5000 ironheads were investment cast with the scorelines in the faces from the casting process after which each face was precision computer machined to a condition of flatness within a tolerance of 0.001″. A milling pattern was chosen which created a ridged texture on the entire face that increased the friction between the face and the ball in an effort to enhance backspin on the ball. However, perhaps the most significant part of the manufacture of the CMC5000 was that after face milling the irons still had consistent USGA conforming score lines.
Given the nature of face flatness variations from the investment casting process, machining the face after casting could have created wide variations in the width and depth of the lines on the face. To manufacture the CNC5000 irons, the casting process had to be improved to make a very flat face right out of casting so that when the faces were machined, the scorelines were still consistent and USGA legal.
Notably, the CNC5000 irons represented the first time a full set of irons had been made with milled faces, a technique even today that is relegated only to some companies’ wedges.
First ironset with progressive topline thickness for vertical centre of gravity change
1996 – Golfsmith XTR II Plus Irons
In a design shape and style that Tom later admitted was a bit too visually different for most golfers to accept, the XTR-II ironhead set represented a design in which the topline width was designed to be thin on the long irons (3.5mm wide on the #1-iron) and then allowed to widen progressively on each ironhead through the set (12mm on the wedges).
Through this design feature, it was possible to keep more of the head mass lower in the head for a lower CG in the long irons, while progressively moving the CG higher to offset hitting the ball too high as loft increased to the short irons and wedges. A number of later designs such as the Cleveland Micro-Cavity irons in which weight is removed from the topline to enhance the CG location stand as a low to high weighting concept pioneered initially in a Tom Wishon iron design. In addition the XTR-II irons were the first to remove weight from the hosel to make it easier to locate the CG in the center of the scoreline area. The hosel was designed with thin wall vertical grooves to reduce its weight.
First titanium iron with bi-metal construction
1997 – Golfsmith MWD1000 Irons
The first introduction of titanium alloy irons had a short life in the golf industry, chiefly because a full set sold for nearly $2000, second because the first sets introduced by Tommy Armour Golf were hugely larger in blade size than what golfers were comfortable with playing. From Armour’s design many golfers had the impression that because titanium was lighter than steel, all titanium irons had to be overly large. While the huge head size did have a very high MOI, its size was simply unacceptable for the vast majority of golfers.
When formed into a hollow body, thin face woodhead, a titanium design performs better than any other metal wood because its high strength to modulus ratio allows for a faster ball velocity off the face. However, when a titanium alloy was formed into a solid body construction for an iron, the spring face capability is eliminated because of the thick face section. In addition the low density of the titanium requires the head to be extremely large to achieve normal iron head weights.
The MWD-1000 irons recognized that the potential for Titanium in an iron design could only be realized by designing the head as close as possible to a normal ironhead size, then employing the use of heavy density weights attached to the head to achieve normal headweight and to improve the perimeter weighting and CG requirements of a game improvement ironhead design. Thus the MWD-1000 irons became the first solid titanium alloy ironhead to utilize a second high density metal (brass) in the design to allow the creation of a more normal size head with greater perimeter weighting (MOI).
First iron with multiple face thickness variations for CG and weight distribution control
1998 – Golfsmith Jetstream 2 Irons
In 1998, Tom had discovered that moving the center of gravity (CG) 2mm to 3mm toward the heel side of the center of the face would allow the golfer to more effectively rotate the club back to square on the downswing and thus reduce the chance of pushing or fading the ball. For some time, it had been agreed by all club designers that a lower CG was preferred for average to less skilled players. Prior to this time, investment cast stainless steel irons were always made with a uniform face thickness of 3mm to facilitate consistency in flow of the molten metal the investment casting process so the center of gravity (CG) position had to be controlled by the height of the blade or the width of the sole.
The Jetstream 2 irons were designed with different thicknesses over different areas of the face –the upper toe area was reduced to 2mm and the lower toe area to 2.5mm to keep weight from being high on the head and too far from the shaft. The bottom areas of the face were increased to 4mm thickness to help move the CG lower in the head. Thus the original height of the blade and sole width could be retained while still being able to manipulate the position of the CG in the head. This design required very precise production dies to be made to ensure the accuracy of the face thickness design in the casting process to be able to move the CG to the desired position lower on the head and a little closer to the shaft to offer golfers more control and accuracy.
First iron with aluminium alloy body
1998 – Golfsmith TG System Irons
Tom knew from his previous experience with designing the titanium + brass MWD1000 irons that a key element in iron performance was to be able to re-position as much of the head’s total mass in specific areas of the head to improve off-center hit forgiveness (MOI) and/or to lower the center of gravity (CG) to increase the launch angle of the shot and make the iron easier for less skilled golfers to hit well up in the air to fly. To gain the most mass possible to move to desired areas of the iron requires that the body of the iron be made from the lightest material possible that is still able to withstand the force of impact.
The predominant metal used in the manufacture of ironheads since irons were first invented in the 1700s has been steel. However, steel is a high density material. For their basic shape and size, steel ironheads allow very little additional mass to be left over to be re-positioned on the head to enhance the MOI or change the CG location. While titanium irons were developed in the late 1990s did allow mass to be positioned on the head for MOI improvement, their much higher cost soon proved that golfers simply would not pay that much for a set of irons.
Because irons are subjected to far less impact stress than woods, Tom decided to turn to a high grade aluminum alloy to construct the body of the ironhead. Because aluminum has a density less than half that of titanium and 70% lower than steel, an aluminum body iron would allow a tremendous amount of the total weight of an ironhead to be able to be moved to areas on the head which would greatly increase the MOI and lower the CG.
The TG System irons were truly an innovative advance in clubhead production engineering. They were designed and manufactured with a stainless steel sole and twin heel and toe located tungsten weights on the back to lower the CG and increase the MOI. In addition, the face of each TG System iron was plasma coated to give the face the required durability. Thus the TG System irons became the first aluminum body iron ever designed and offered a greater amount of weight distribution enhancement than any iron yet made.
First iron designed with progressive head height from shallow in the low loft irons to traditional in the high loft irons and wedges
1999 – Golfsmith Contour PLP Irons
From having designed numerous iron models Tom knew that the predominant factor that controls the vertical center of gravity in an iron is the height of the clubhead. Making an ironhead taller significantly moves the CG higher in relation to the ground.
It’s quite obvious that the lower the loft, the more difficult it is to generate a higher launch angle to create a high enough shot trajectory to maximize distance for the lower loft irons in a set. At the same time a higher CG can be more beneficial in the high loft irons and wedges to counter the effect of the much higher loft toward hitting the ball too high and losing distance or making the shot more susceptible to the effect of wind.
Knowing that he wanted to design a game improvement set in which the CG was as low as possible in the low loft irons but progressing to a much higher CG in the high loft irons and wedges, Tom had the thought to incorporate a progressive head height through the set in which the lowest loft irons would progress from a shallow face profile not unlike the old shallow face Browning 440 irons of the 1970s. Through the set the head height would gradually increase until reaching a slightly taller than normal game improvement head height in the high loft irons and wedges.
The Contour PLP irons delivered a much lower CG in the #1, 2, 3, 4 and 5 irons than what was typical in a game improvement design of traditional shape and profile through a head height that was 7mm to 12mm more shallow than the typical blade heights of a game improvement design.
First iron made from aluminium alloy body with steel sole and tungsten weighting
1999 – Golfsmith TG System Irons
The predominant material used in the manufacture of iron heads since began with iron, changing later to steel not long after ferrous alloys were developed. Steel is a high density material. When made to a normal size acceptable to golfers, solid body steel iron heads allow very little additional mass to be left over to be positioned on the head to increase the MOI or change the CG location. While the few titanium iron models developed in the late 1990s allowed more mass to be located in different areas on the head to increase the MOI or customize the CG, the much higher cost of titanium proved that golfers simply were not willing to pay that much for a set of irons.
Because irons are subjected to less impact stress than woods, Tom decided to turn to a high grade aluminum alloy to be able to construct the body of the ironhead from a very light material and offer the potential CG customization and an increase in the MOI. Because aluminum has a density 40% lower than titanium and 70% lower than steel, an aluminum body iron would allow a tremendous amount of the total weight of an ironhead to be able to be moved to areas on the head which would significantly increase the MOI and lower the CG. The high strength aluminum alloy head body comprised only 25% of the total weight of each Tg System iron head; the rest of the head weight came from the steel sole and the twin tungsten heel and toe weights.
However, even high strength aluminum alloys are extremely soft and highly susceptible to developing deep scratches and dings from impact with the ground or shots hit from sand. To lower the CG and to provide adequate durability on the sole, Tom designed a steel sole piece that the high grade aluminum would be cast around to secure on the sole to offer adequate durability for the sole as well as to lower the CG. To achieve proper durability for the face, a plasma material was sprayed on the face. To increase the MOI, toe and heel tungsten weights were press fit into the back of the head.
The TG System irons represented a truly innovative advancement in clubhead engineering to offer a greater amount of weight distribution enhancement than any iron yet made.
First thin face forged steel set of irons
2000 – Snake Eyes Fire Forged Irons
Because of his significant experience designing numerous thin face drivers during the 1990s with a high strength steel face to achieve a higher Coefficient of Restitution (COR), in the late 90s Tom went to work to determine if it could be possible to design an iron with a higher COR to offer golfers more distance. This was a difficult task because of two primary reasons: 1) as loft increases, the ball cannot flex the face inward as much to generate a higher ball velocity, and 2) irons are typically designed with an asymmetrically shaped face. Clubheads with a more symmetrical shape face such as drivers are far easier to design to enable the face to flex inward more from impact with the ball.
By working with a technically astute clubhead production foundry which also had the ability to formulate experimental steel alloys to achieve different mechanical properties, Tom spearheaded the task to create a new high strength steel alloy with yield strength in excess of 250KSI but also with slightly more elasticity (lower modulus) than other steel alloys used in clubhead design. This HS300 custom steel alloy was then true forged at a thickness of only 2.1mm to create the faces which were welded to the body of the head to create the Snake Eyes Fire Forged irons.
Tom had previously designed iron models with a titanium alloy face but neither of these models were conceived in an attempt to create a high COR face design; the Ti face was used to make the face lighter to create more weight to position on the perimeter of the head to improve the MOI. The Snake Eyes Fire Forged irons were the first conscious attempt to design an iron with a thin high strength alloy face for a higher COR.
Testing with the Fire Forged thin, high strength steel face irons showed an increase in Smash Factor (Ball Velocity divided by Clubhead Velocity) over previously designed thick face irons. Air cannon COR testing showed the Fire Forged irons had a COR of 0.805, compared to the typical 0.775 COR of a conventionally made investment cast stainless steel or forged carbon steel iron. While not quite at the 0.830 limit for COR imposed in the rules of golf, the Snake Eyes Fire Forged irons represent the first successful attempt to create an iron with a higher COR.
First forged iron to incorporate a 5-step forging process; first forged irons to offer mix and match set makeup between matching muscleback and cavity back design
2003 – Wishon Golf 550C & 550M Forged Carbon Steel Irons
In 2002, Tom was asked by one of the leading clubhead production foundries to help solve a problem for one of the foundry’s other golf company customers. This company was trying to promote a new forged carbon steel iron on the PGA Tour but had been receiving criticism from a number of the tour players that the face profile shape, particularly at the leading edge position of the heads was too inconsistent.
After researching the problem, Tom determined the inconsistency in the shape of the leading edge occurred because the foundry’s workers were occasionally grinding too much off the bottom of the sole directly under the leading edge as they worked to remove the wide flat section left from the shearing off of the excess steel after the typical 4th and final step in the forging process.
By making a 5th die, and forging the heads one more time, the area and amount of excess metal under the leading edge of the face which had to be ground to blend with the sole radius was greatly reduced to a very small and narrow section of steel. The workers could easily grind off this smaller flashing line of excess steel without changing the profile of the leading edge. The result was the foundry could now deliver heads which demonstrated a very high level of consistency for overall face profile shape. In addition the 5th forging step allowed the raw forgings to demonstrate a tighter weight tolerance which helped improve the final weight tolerance of the finished heads.
However, an additional benefit of adding a 5th step to the forging process was not realized until Wishon Golf’s 550C and 550M forged cavity and muscle-back irons were being designed and tested in the fall of 2002. While the 550’s displayed the same high level of face profile consistency known to come from the additional forging step, golfers involved in the testing of the 550’s reported a much softer feel of impact than they had ever felt with previous forged carbon steel irons.
Electron microscope photomicrograph analysis showed that by forging the heads one more time, the additional 5th forging step had compressed the steel in each head much tighter than was possible from the previous 4 step forging process. This 5th forging step thus had the effect of greatly reducing the natural ‘voids’ (microscopic holes) inside the grain structure of the steel that are present in all forged ironheads. By eliminating a huge number of these voids, the internal vibrations from impact were also reduced, which had the effect of transmitting a softer and more solid feel to the golfer.
Word of this change in the forging process soon circulated around the golf industry and by 2004, other golf companies were marketing the claim that ‘their new 5-step forging process made their forged irons better and softer feeling.’ In truth it was Tom Wishon who first brought this production improvement to the forging process.
In addition, the 550C and 550M were consciously designed to offer golfers a mix and match set makeup between the 550M muscleback and 550C cavity back models. To facilitate a custom set makeup design the head sizes and the CG positions of all like number irons in each version were designed to be identical. With this feature no matter where the break between muscleback and cavity back was chosen by the golfer, the launch angle and spin were accurately progressed for more consistent shot shape and ball flight. The only difference between the muscleback and the cavity back models was the higher MOI of the cavity back for better off-center hit ball speed and distance. No other sets of irons were designed with such precision to create a precision mix and match set makeup.
First variable thickness face set of irons
2004 – Wishon Golf 770CFE Irons
Shortly after he launched his own company, Tom wanted to go back to work on designing an iron model with a higher COR iron than his first attempt at this area of clubhead performance technology in 2000, the Snake Eyes Fire Forged Irons. While the Fire Forged thin face irons did prove it was possible to push the COR of an iron higher than had been previously seen, their COR of 0.805 was measurably, but only marginally, higher than the typical 0.780 COR of the majority of the investment cast stainless steel irons on the market.
In addition, the Fire Forged irons were made with a high strength steel face that was produced with the same uniform thickness over the entire face area. Wishon’s experience with having designed variable thickness faces for various driver head models in the late 90’s also prompted him to speculate if the same type of ‘thicker center/thinner perimeter’ face construction could be utilized on an iron design to improve off-center hit performance. However, the challenge was how could the COR and off-center hit performance be improved for each iron in the set. From the 3-iron to the PW, loft increases incrementally by a total of more than 25 degrees. As loft increases, the impact force necessary to flex the face inward to achieve the higher COR decreases proportionally.
To allow each 770CFE (CFE =computer face engineered) iron to perform as close to the same as possible with respect to their face deflection, Wishon employed the use of three different steel alloys of different strength to progressively increase the faces’ ability to flex inward as the loft increased. In addition, as the loft increased for each iron through the set, each iron’s face was made progressively thinner to allow each higher loft face to flex inward close to the same as each other iron.
For the variable thickness face, Wishon also knew as loft increased through the set, the actual point of typical impact on the face changed slightly; as loft increases the point of impact rises higher on the face. Thus for each iron, the thicker center section had to be positioned in a slightly different area of the face plates. This type of design required very tight tolerances for the face thickness of each iron. To meet that challenge each face was CNC machined to its specific thickness dimensions to a tolerance of 0.05mm (0.002″). The following CAD image shows the different variable thickness faces of the 770CFE and how the position and size of the thicker center area moved from low and smaller on the low loft irons to higher and larger on the high loft irons.
While this work pushed the measured COR of the 770CFE irons to 0.815, the other significant benefit was the performance of the variable thickness face for improving off-center hits. Shots hit off center resulted in a loss of only 2.5% of the on center hit ball speed.
The 770CFE irons were recognized as ‘the most innovative new iron’ of 2004 by Golf Illustrated magazine and also achieved Golf Digest Hot List recognition as well. The first variable thickness irons offered by a major golf company were introduced two years after Wishon Golf introduced the 770CFE.
First iron with cnc milled back cavity to increase MOI; first forged iron to achieve an moi as high as an investment cast cavity back iron
2007 – Wishon Golf 560MC Forged Carbon Steel Irons
For decades, forged carbon steel irons were relegated to a muscleback shape with no cavity on the back. Their off-center hit performance was virtually non-existent because of the very low MOI of the muscleback weight distribution.
In response to traditional golfers’ request for better off-center hit performance, the industry introduced the first cavity back forged carbon steel irons in the 1980s. While their off-center hit performance was better than a pure muscleback forging, that game improvement aspect of the forged cavity back iron fell well short of what was possible in the very deep cavity back style of investment cast stainless steel irons. In the forging process, the depth of the back cavity is very limited. In a forging, metal is ‘pushed around’ the head and never actually removed or poured into a shell as it is with a cast stainless iron. Thus it is impossible to make a forged iron with as deep of a cavity and as high of MOI as is easily achieved with investment casting.
Motivated by a desire to figure out a way to offer the best of both worlds to golfers who wished to play a forged carbon steel iron, Wishon began to think what might solve the problem to allow the back cavity on a forged iron to be as deep and thus make the head as forgiving for off-center hits as a cast iron. The answer came from the simple question of, ‘how can we actually carve more metal out of the back of this forged iron to increase its MOI and off-center hit performance while retaining the same soft feel of a forging?’
Above: the original 560MC irons introduced in 2007. Below: the second generation 560MC irons introduced in 2012.
The 560MC forged irons began production as a raw carbon steel forging with a flat back with no weight distribution shape on the back of the raw forging. After forging, each head was placed into a CNC machining center which literally carved the entire deep back cavity from the back surface of the raw forged head. The result was the 560MC irons not only had the deepest cavity of any forged iron previously made, but their MOI and off center hit performance was much higher than any other forged cavity back iron.
MOI measurements of 5-irons showed the MOI of a forged muscleback was 1050g/cm2, the MOI of a forged cavity back was 2025g/cm2, while the MOI of the forged 560MC #5-iron was 3075 g/cm2. (MOI measured about the vertical axis through the CG)
First set of all hybrid body construction irons
2008 – Wishon Golf 785HF Hybrid Irons
During the development of the high COR 785HF hybrids, Tom began to think that while it was nice to offer a #2, 3, 4 and 5 hybrid in the 785HF design to allow golfers to replace their lower loft irons, it might also be beneficial if the 785HF set could be expanded to allow less skilled golfers and slower swing speed golfers a chance to replace their entire set of conventional irons with a full set of high COR hybrids, all the way through the Pitching Wedge.
Golfers with slower swing speeds and golfers who are not skilled at hitting down and through the ball with their conventional irons struggle to get the full distance possible from their swing speed when hitting a conventional iron. This is chiefly because the center of gravity (CG) of a conventional iron is always very close to the face. It is also known that the lower and farther back the CG from the face, the higher the launch angle of the shot can be, and from that, slower swingers can generate more distance by getting the ball to fly higher.
As a result, Wishon decided to expand the high COR 785HF hybrid design to include a full set option from the #2 all the way through the #9 and PW. In doing so, in 2008 when the 785HFs were introduced, they not only represented the industry’s first high COR hybrid, but the industry’s first full set of high COR hybrid body irons all the way through the Pitching Wedge.
First set of irons with variable thickness titanium face to achieve the maximum 0.830 COR
2009 – Wishon Golf 870ti Irons
If there is one thing that is true about Tom and his work, he is rarely 100% satisfied with any of his clubhead designs. A few years after designing the 770CFE high COR, variable thickness face irons, Tom began to think about the 0.815 COR of the 770 irons and wonder if something could be done to push the COR to the USGA limit of 0.830. Knowing that titanium alloys possessed a higher strength to elasticity ratio than any high strength steel alloy, and realizing titanium has a 40% lower density than steel Tom began to work on designing a set of irons with a thin, variable thickness construction face made from a high strength titanium alloy.
There is no question sets of irons with a titanium face had been introduced in the golf industry in the late 1990s. Tom himself had designed a Ti face iron set for the Harvey Penick line of custom designed clubheads during that time. But all previous Ti face irons were designed with the same 3mm thick face as was being used in titanium drivers. A 3mm titanium face in a driver can come close to the limit for COR because of the larger face area and lower loft. In an iron with a smaller, asymmetrically shaped face and more loft, the same 3mm thickness will not bring about an increase in COR because the amount of face flexing at impact is greatly reduced by the odd face size/shape and higher lofts.
The only technical focus of the early Ti face irons was to use the lighter weight titanium face to gain discretionary weight to position in other areas of the head to improve the MOI and off-center hit performance or to customize the CG. By replacing the steel face with a titanium face, 40% of the weight previously used in the steel face was now available to be re-positioned elsewhere on the head to improve the MOI or change the center of gravity (CG) location.
Tom’s concept was to basically duplicate the thin, variable thickness steel face design of the 770CFE irons but with a higher strength beta grade titanium alloy for the face. Through this, Tom felt the higher strength to elasticity property of the titanium could increase the COR of the face, and the reduction in the weight of the face through changing from steel to low density titanium would additionally allow the MOI of the 870Ti irons to be higher than the MOI of the 770CFE irons for even better off center hit performance.
During a trip to speak at various European PGA educational programs in the summer of 2008, Wishon brought a final 870Ti iron prototype to a meeting he had with the technical department of the Royal & Ancient of St Andrews. After the meeting, Wishon asked the R&A to conduct a COR test on the 870Ti prototype iron. The test showed the 870Ti had an actual COR of 0.829, which proved Tom had been able to achieve his goal of improving the COR of an iron from the 0.815 level of the 770CFE to reach the limit in the rules.
First set of irons with changeable head number
2009 – Wishon Golf 752 O/S Irons
Prior to the 1980s there actually was an informally agreed standard in the golf industry for loft in the design of irons. No matter the company, the 1-iron had a loft of 17*, the 2-iron was 20* and then each iron through the SW increased in loft in increments of 4*. Starting in the 1980s various companies began to break ranks and begin to lower the lofts of their irons, chiefly as a means to sell more sets on the basis of promising more distance in a very competitive industry that was beginning to become crowded with golf equipment companies.
Tom has always been highly critical of this trend because it is rooted in a desperation by companies to simply sell more product by preying on the lack of technical awareness of golfers who when hitting a new model iron longer than the same number iron in a previous model are easily fooled into believing the reason for the distance increase is from a technical breakthrough by the company. While some companies attempted to defend their move into lower lofts on their irons as needed to offset the effect of a lower CG, the explanation was exposed as false when it became apparent that when each club in the bag from driver to sand wedge is hit square and on-center the height of all shots is the same.
Tom’s main area of protest against the industry’s trend to lower iron lofts was the fact that when the first company deviated to lower the lofts of each iron in a set, every company had to do the same or risk losing sales when golfers would hit the lower loft sets and think they were superior to other models with higher lofts per head number. Clubmakers had begun to tell Tom that they had lost sales of Wishon model irons when their customer hit shots longer with a lower loft model from another company for the only reason that the lofts were lower.
Tom admits that the primary reason he designed the 752 O/S irons with the ability to allow the Clubmaker to install the choice of head number on the sole of each iron was as a protest to the golf industry’s trend to continually lower the lofts of irons as a means to sell more sets. If the consumer golfer told the Clubmaker he hit the XYZ iron longer than a Wishon iron, the Clubmaker could offer the 752 O/S model and simply switch the sole number higher to allow the golfer to hit the same number iron in the 752 O/S as far or farther than the other company low loft iron.
Unlike Tom’s other clubhead design firsts, there were no technical advances in the design of the 752 O/S irons. But because no other iron had ever been designed with interchangeable sole numbers, the 752 O/S weakly earns its place on this list of design firsts!
First high COR face irons with carbon steel body for a wider range of loft and lie fitting capability
2013 – Wishon Golf 771CSI Irons
While both of Tom’s previous high COR iron designs (770CFE & 870Ti) garnered high reviews from clubmakers and golfers for their high smash factor and off-center hit shot performance, Tom had always disliked the fact that both models had been forced by the production factory to use rigid, virtually unbendable 17-4 stainless for the body of the irons. Without any previous experience in manufacturing a thin face high COR iron, the production factories feared that the faces could potentially come loose if the heads were bent substantially for a loft or lie change and thus insisted on making the body of the 770CFE and 870Ti from 17-4 stainless steel.
By 2013 Tom was able to convince the production factory that had manufactured the 870Ti to make Tom’s next generation high COR face iron with a carbon steel body. The factory was well aware of the importance of a Wishon Golf iron design to be able to be bent to a reasonably wide range of lie and loft fitting specifications so they agreed to investment cast the body of the 771CSI irons from 8620 carbon steel alloy.
The result was a new super game improvement iron design with the face as close to the USGA/R&A limit for spring face performance as possible but with the ability to be adjusted within a wide range of +/-4* for lie or loft fitting requirements.
First set of single length irons designed to be played at 8-iron length; first single length iron set with mixed high COR/Standard COR construction
2016 – Wishon Golf Sterling Single Length Irons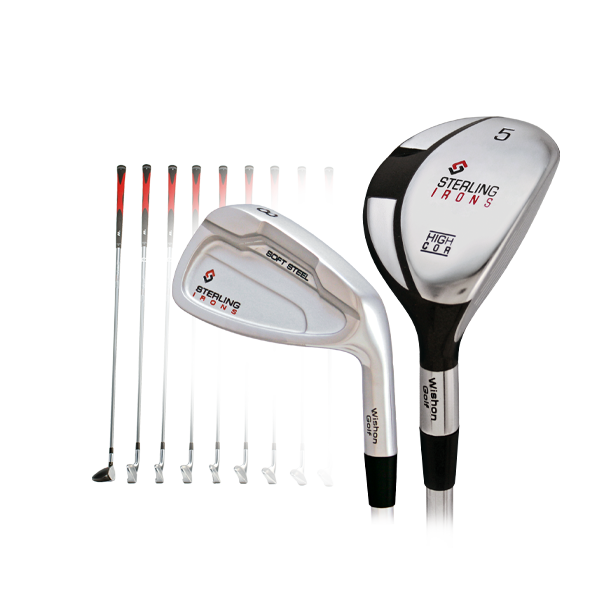
While Tom had taught clubmaking to the founder of the golf industry’s first company to exclusively sell a single length set of irons (Eric Cook – Iso-Vibe Canada) in 1986, Tom had never considered tackling a single length iron design because he felt the awareness and demand was too small to make the effort worthwhile. Besides, with every previous single length set being made to a 6-iron length of 37.5” to ensure the low loft irons could be hit as far as their conventional length counterparts, Tom felt that a 6-iron length was too long for the majority of golfers to be able to control and hit normal distances with the high loft irons and wedges.
In the fall of 2013 an American PGA professional based in Europe traveled to meet Tom to try to convince him to think outside the box to design a new set of single length irons that could incorporate modern iron design technology. At first Tom was not interested but when the PGA professional asked if a new single length set could possibly be designed to a shorter length than a 6-iron, the light almost literally went off over Tom’s head.
With four different high COR face iron designs under his belt, Tom had the thought that if the set were created with a high COR face for the low loft irons and matched with a conventional face design in the high loft irons and wedges, it could be possible to make a single length set to a shorter length and still achieve proper distances for all the irons in the set when compared to a conventional incremental length set of irons.
With the direction of the design in mind, Tom began to design a new single length mixed face set of #4 to 7 iron with high COR faces matched with conventional cast carbon steel one piece #8 through the wedges. Tom chose an 8-iron length for the single length irons from the thought that not only would an 8-iron length be easy for most golfers to hit more consistently on-center but it would allow the wedges to be more easily hit to normal distances and not too far as had been a problem with 6-iron length single length sets.
The Sterling Irons were also the beneficiaries of good timing when in 2015 Bryson deChambeau with a single length set of irons became only the 5th player in history to win the NCAA and US Amateur titles in the same year. Almost overnight the golf media couldn’t write enough about the unusual set of single length irons that had been used to win two of the world’s most prestigious amateur titles. Bryson’s use of a set of irons made to the same length single handedly broke down the opposition and doubt that had previously accompanied single length irons to enable a credible demand to become established for irons made to one length.
The Sterling Irons were introduced in spring 2016 and went on to become the greatest selling set of irons ever offered by Wishon Golf.
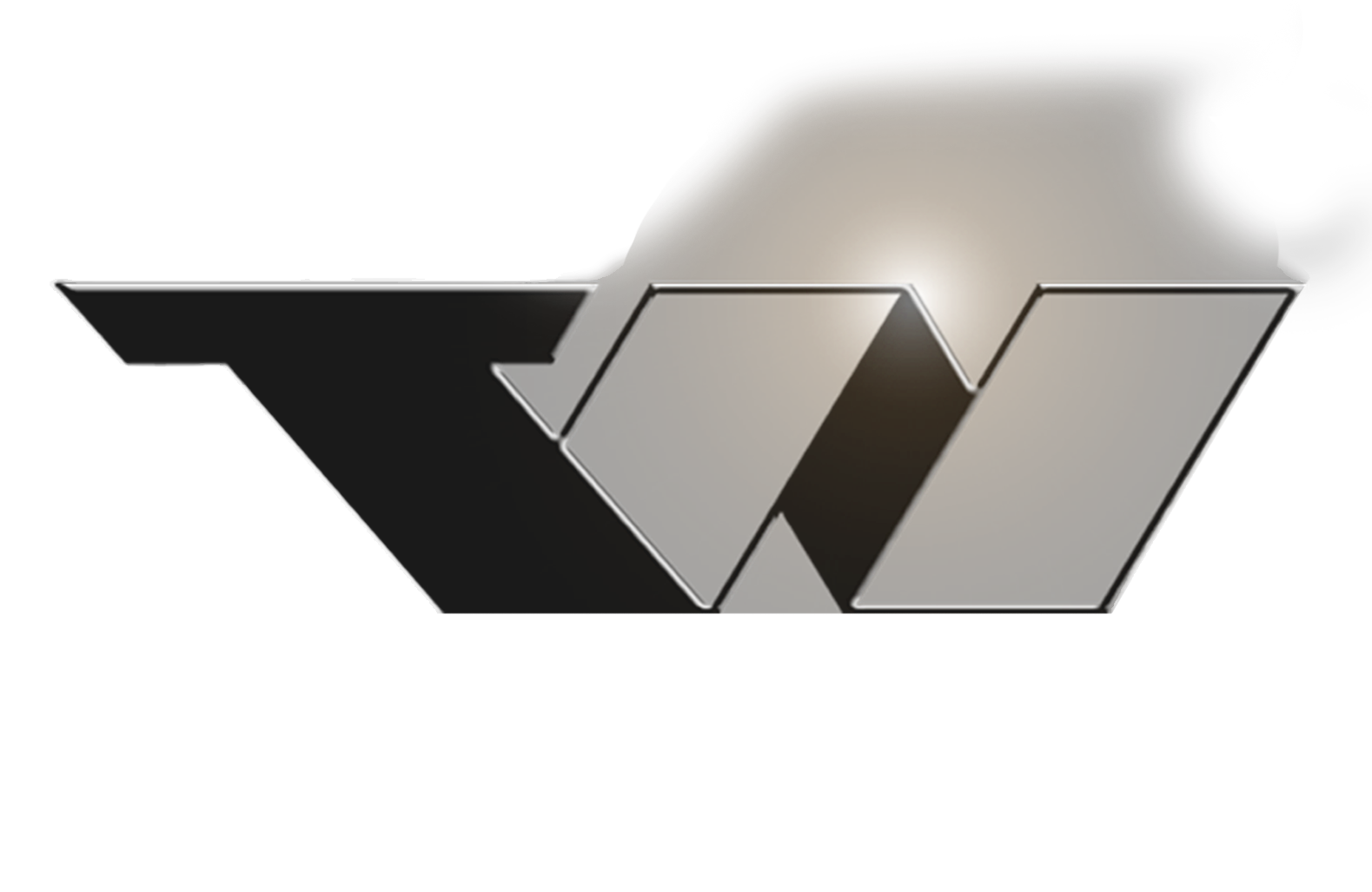
© COPYRIGHT 2025 WISHON GOLF